January 8, 2024
New year, new case study to share: BMA Braunschweigische Maschinenbauanstalt AG
For over 170 years, BMA AG has been a well-known supplier to companies involved in the industrial production and refining of sugar. The company itself develops, manufactures and installs the full range of machinery needed to perform all of the core processes of sugar production. From extraction and evaporation to crystallisation and drying, BMA’s product range can provide the ideal equipment required. In addition to its headquarters in Braunschweig, Germany, BMA has subsidiaries in China, Tunisia and the USA.
“As well as manufacturing our own products, such as centrifuges, we make our comprehensive fleet of machinery available to other companies on a contract manufacturing basis,” explained Jens Dohnalek. Any enquiries can be sent to the company’s e-mail address: [email protected]. Dohnalek joined BMA in 1987 and since 2018 has been Production Manager for mechanical machining, mechanical engineering, drum manufacturing and electrical and control cabinet construction at the company. The CNC machines from Unisign are also located in his department.
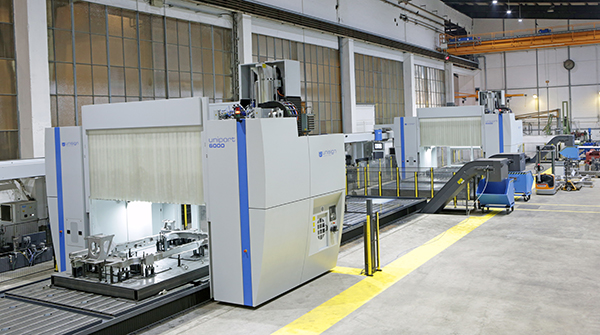
Retrofitting
BMA purchased its first Unisign machine in 1993 – a UNIPORT5 and a UNIVERS6. Two years later, it then took delivery of its first UNIPORT6 machine, which just like the UNIVERS has been in operation ever since. In 2018, the company expanded its fleet of machinery once more with the purchase of two UNIPORT6000 machines. As Jens Dohnalek explained: “The UNIPORT6 machine we bought back in 1995 is basically still fine, but it needs to be renovated in a few places, so we plan to have it retrofitted this year. That is one of the additional services that Unisign offers.”
Less stress
Dohnalek continued: “The first time we were in contact with Unisign was at a trade fair. We were looking for a relatively large CNC machine for the machining of a specific product with a diameter of 5.60 metres and we opted for the UNIPORT5. The UNIPORT6 that we bought back in 1995 replaced a table-type boring machine. We wanted to machine multiple surfaces using a right-angle head with less stress.”
Ever since then, BMA has chosen Unisign as its machine supplier time after time. Dohnalek said: “The level of service we receive from Unisign has always been good. For example, a right-angle head can sometimes break if you don’t handle it carefully. When that happens, Unisign loans us a right-angle head so that we can resume production as quickly as possible. Unisign’s ability to provide spare parts was actually a key factor in our decision to order our new CNC machines.”
Machining that is cost-effective
BMA machines large quantities of various components made of steel, stainless steel (or duplex stainless steel) and cast materials on its UNIPORT6000 machines. Dohnalek told us: “The workpieces that we machine include items such as centrifuge components, housings, scaffolding trestles, tube plates, support plates and tubular shafts and these machines are able to accommodate larger components. For us, that’s very important, as it enables us to machine welded assemblies completely. That wasn’t the case before. We had to do the mechanical machining first and the welding afterwards. That was a big disadvantage.”
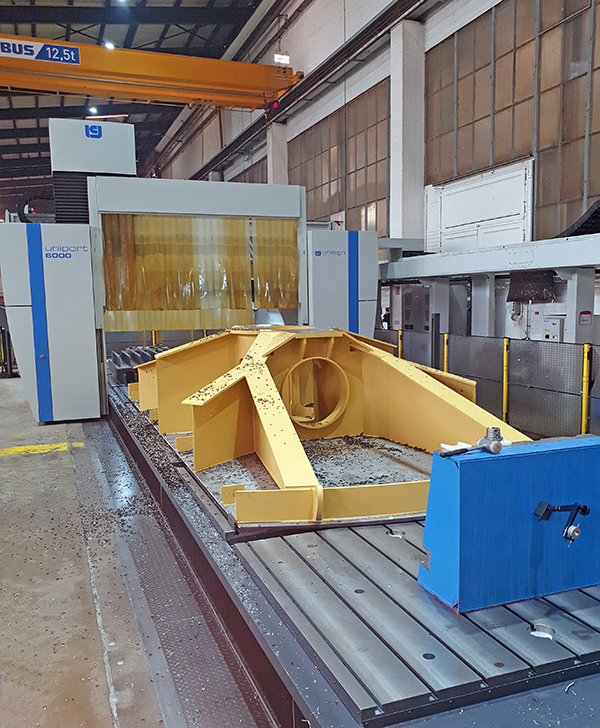
Double table
BMA made a conscious decision to purchase UNIPORT6000 machines that offer pendulum machining. Dohnalek explained why: “Previously, we had machines with a table that was limited to work pieces measuring 6 metres. Now, we have two Unisign machines and each one is equipped with a double table that is 14 metres long. The working area has been divided into two, which means that we can operate using a parallel set-up. And those 14 metres certainly make all the difference when machining long components.”
Tool places
For BMA, the UNIPORT6000 machines have proven beneficial in a number of ways. Dohnalek particularly appreciates the higher rapid traverse, the shorter tool change and right-angle head change times and the increased availability that is provided by two identical machines. The large tool magazine also offers several key advantages. Dohnalek said: “In each machine, we have 197 tool places. Normally, machines have only 27 places as standard. Unisign increased the number of tool places especially for us. As we machine a variety of materials, we also need a variety of tooling.”
Maintenance contract
When it comes to Unisign, Dohnalek feels well looked after: “I’m certainly very content with the level of service. When something isn’t right, the first thing we do of course is ask our own in-house specialists from our maintenance department to take a look. They are the ones who make the initial diagnosis whenever a fault occurs. But if they can’t progress any further, Unisign is on hand right away. What is more, we also have our own work preparation department that is responsible for programming the CNC machines. If any issues arise from that department, Unisign is able to give us the support that we need.”
BMA has also signed a maintenance agreement with Unisign to ensure that the necessary maintenance work is carried out and Jens Dohnalek is extremely satisfied with that too. “Unisign is very flexible. If a service appointment is scheduled in the afternoon, for example, production can often resume during the late shift or night shift that same day. In other words, servicing does not cause any major interruptions to our operations. Unisign is always very good at anticipating our needs.”
In focus
Uniport6000
Specification
- X-axis4.000-24.000+ mm
- Y-axis1.500-5.000 mm
- Z-axis1.000 / 1.250 mm